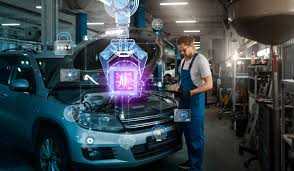
Artificial Intelligence in Car Maintenance
July 23, 2024Artificial Intelligence (AI) can help repair workshops speed up the service for their customers, reduce costs, boost vehicles’ longevity and safety while also providing a more personalised customer experience.
Sophisticated autofocus systems enabled by computer vision allow technicians to do vehicle inspections remotely – the car comes to them instead of the mechanics travelling to the sites. This improves the accuracy of the estimate to the customer and insurance company.
Detection of Defects
Today’s automotive technicians perform the role of a detective, uncovering stealth engineering issues and rapidly diagnosing your vehicle by having access to technology that provides rapid information about your vehicle’s systems.
AI-enabled sensors connect to the on-board diagnostics port – the car’s metaphorical artery giving real-time data to these systems – and run complex algorithms and machine learning models on features of damaged objects to train itself to recognise features on future inspections.
The key feature of the Grad-CAM system is that it explains to the operator the reasoning behind the defect decision, increasing confidence in the result and decreasing inspection error and maintenance. It also helps operators increase inspection accuracy in the same time period while decreasing the downtime that occurs through both inefficiencies in resources and outright breakdown. Finally, it can prevent fraud by helping insurance companies assess claims accurately and quickly.
Predictive Diagnosis
ML algorithms and AI technology can identify signs that there is a possibility of a mechanical failure even before it can evolve into a physical breakdown, enabling shops to schedule a repair at the best moment, thus preventing downtime and customer satisfaction.
For example, say your car was rear-ended on the road by another car; the vehicle would need to be brought into a body shop, which would have to access the underbody and panels to find damage, taking an hour or more – but now, with TeleDiagnostics, machine learning and imaging can access the damage remotely and within seconds, so that customers can submit insurance claims.
Penske uses Preteckt and other AI-powered preventative action solutions to help their customers manage their operations. The combination of preventative action, real-time information and proactive communication minimises downtime and enables high degrees of reliability for their customers. This model delivers lower costs, better performance and longer useful life for components, and increases efficiency and profitability for all involved, whether they are customers or service providers.
Automated Inspection
Until now, inspections have been done by human inspectors, but today, with an AI, camera-powered solution like UVEYE or Tcheck at the disposal of the shop owner, it can scan the underbody of a vehicle, look for penetrating leaks or foreign objects; later, the data gathered can estimate damages and repair time; and all this is done in matters of seconds. AI can also quicken the inspection while accuracy enhances quality assessment and settlement – helping shops deliver quick service while hitting productivity goals and customer satisfaction goals.
By automating functions that human staff take time on, such as scheduling appointments, sending reminders and keeping customers updated with their cases, AI tools can boost efficiency and leave human resources with more free time to attend to the more critical customer-facing roles.
And Ai crunching repair records units could anticipate usage trends and alert shops when unusual parts shortages loomed, or detect correlations between different types of damage when making faster diagnoses of vehicles, and when allocating resources based on current demand patterns.
Data Annotation
From the accumulation of data generated by sensors, instruments and cameras being built into cars, machine learning and artificial intelligence are able to diagnose vehicular problems more quickly than ever before and suggest proactive maintenance to their drivers.
For automotive companies, shifting towards digital quality inspection will aid them in utilising automation to recognise micro-anomalies that go undetected by manual quality inspection, preserving automobiles on the road with minimal downtime, which in turn will minimise customer dissatisfaction, enhance use rates and boost business expansion.
For organisations that want to use AI, this will mean contracting with containerised annotation services employ the same strong data privacy regulations, have compliance controls in place, and enforce Non-Disclosure Agreements. Even more important will be clear, open lines of communication that helps to ensure that problems are flagged and fixed in real-time – be they questions of understanding, such as reconciling the differences between two annotators doing the same job on the digitised data, visual ambiguity in image annotation, or audio mishearing. That way, the final results would be as good as possible.